Faced with consistently poor labor productivity many large construction companies embraced Lean hoping to reverse that trend.
Many large construction companies in the early 2000s embraced Lean as a project delivery approach hoping to reverse productivity rates hovering around 40% in our industry. Many of those same companies lost millions of dollars through poor execution, inconsistent application and lack of commitment to doing Lean the right way.
We saw an opportunity. In 2018, after nearly 2 years of study, refinement and a methodical re-introduction of the practice, Lean2.0 was born — a new term coined and branded by Flintco to describe our approach to Lean. By working the margins, we are gaining incremental efficiencies at every step of the design and construction process. Data from more than 150 active and completed projects validate our simple premise: When done right, Lean works by bringing more certainty around every critical aspect of your project.
What does better construction look like?
Flintco takes Lean to the next level
Calling it Lean2.0 represents our quest for continuous improvement, a hallmark of Lean and The Flintco Ethos. The Lean2.0 mark is suggestive of a 4-story building and represents the Plan-Do-Check-Adjust cycle that is fundamental to Lean; it also represents the familiar sticky notes associated with collaborative planning and the Last Planner® System that reflect our commitment to the Lean value of respect for people. The accent color takes a cue from the Flintco 4 LIFE logo. The tagline Better Construction means working the margins to gain incremental efficiencies at every step, providing more value to owners and is consistent with our company Vision Statement: Unwavering pursuit of the perfect construction experience.
Our 5+1 baseline practice approach makes Lean2.0 different.
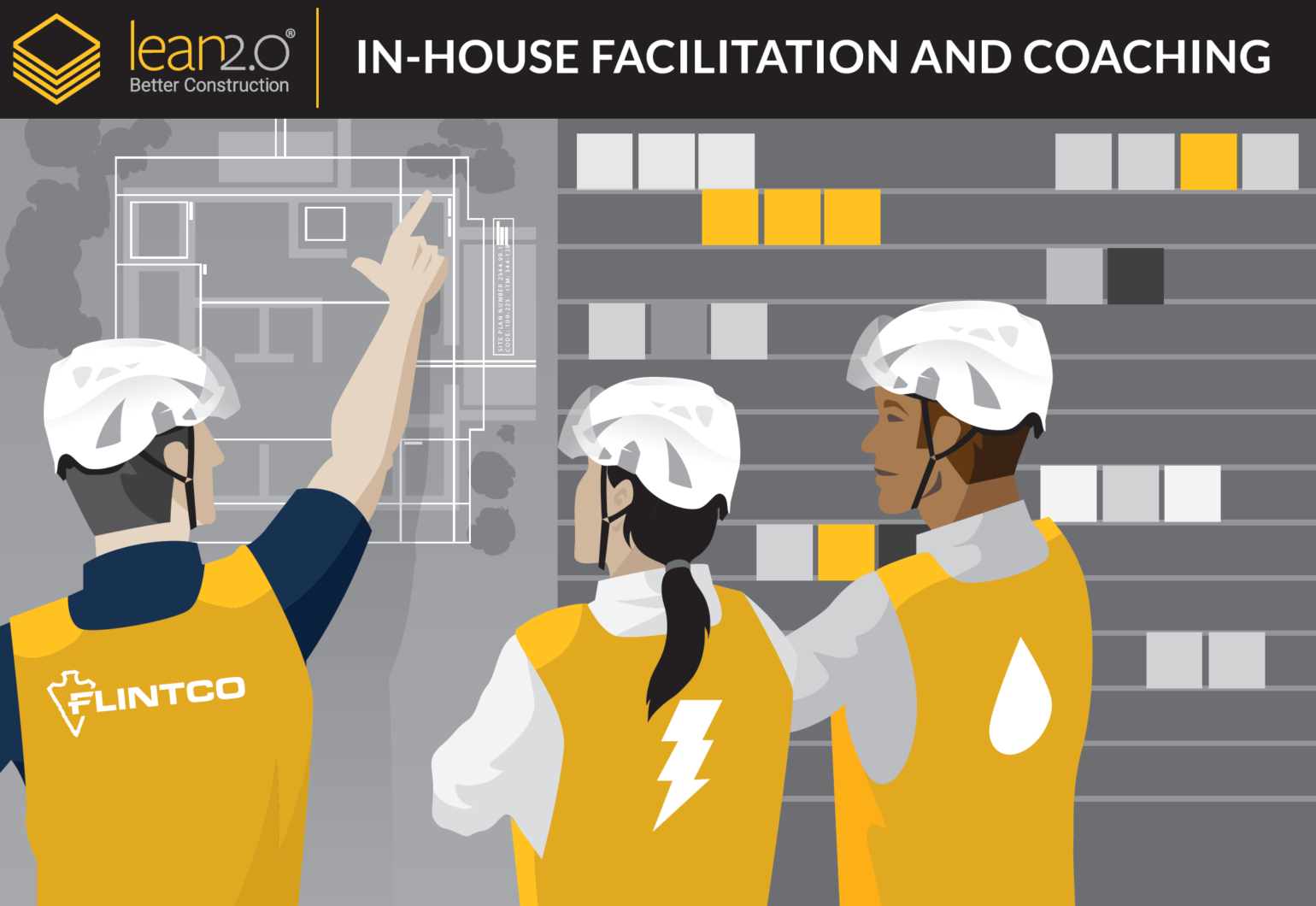
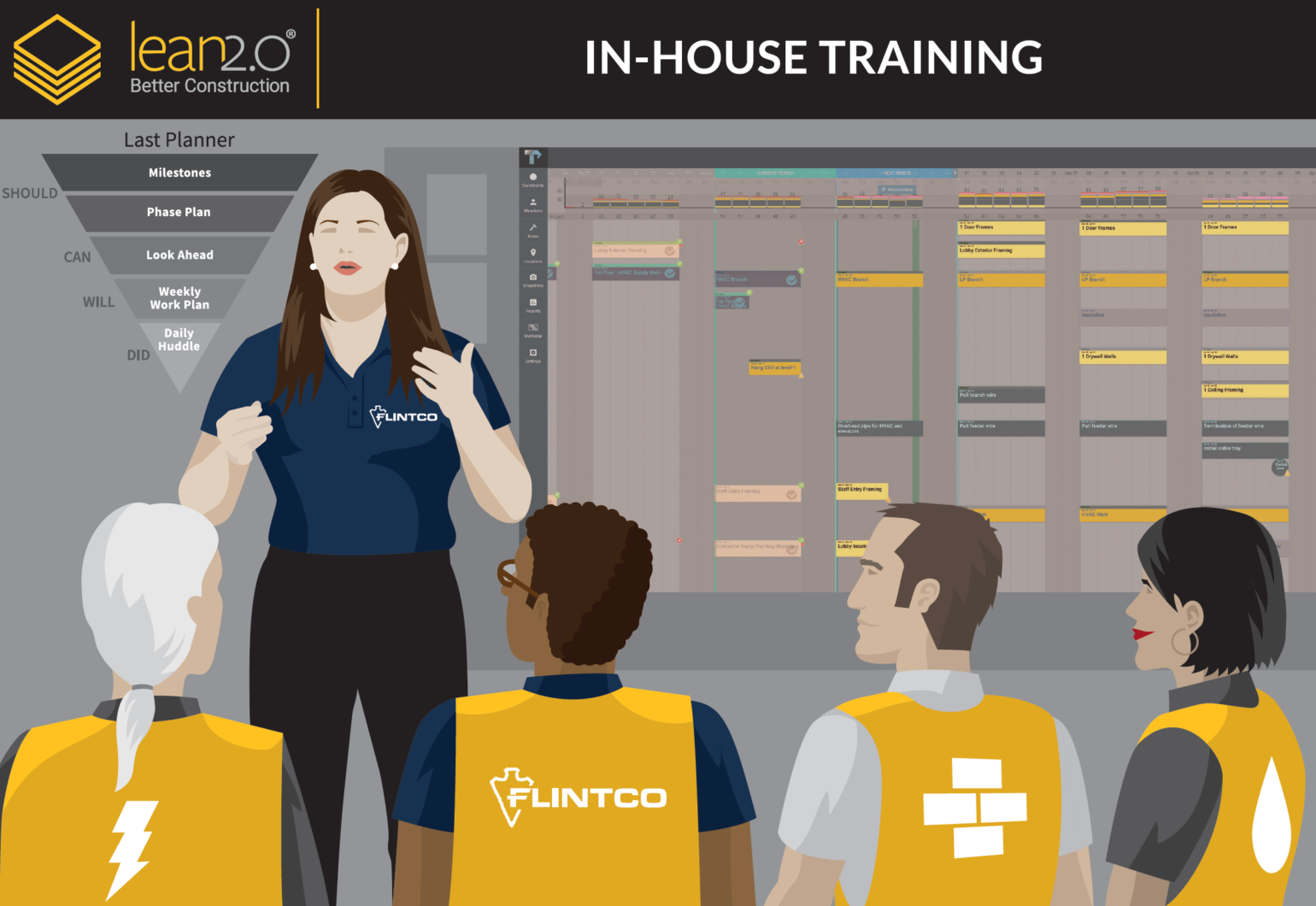
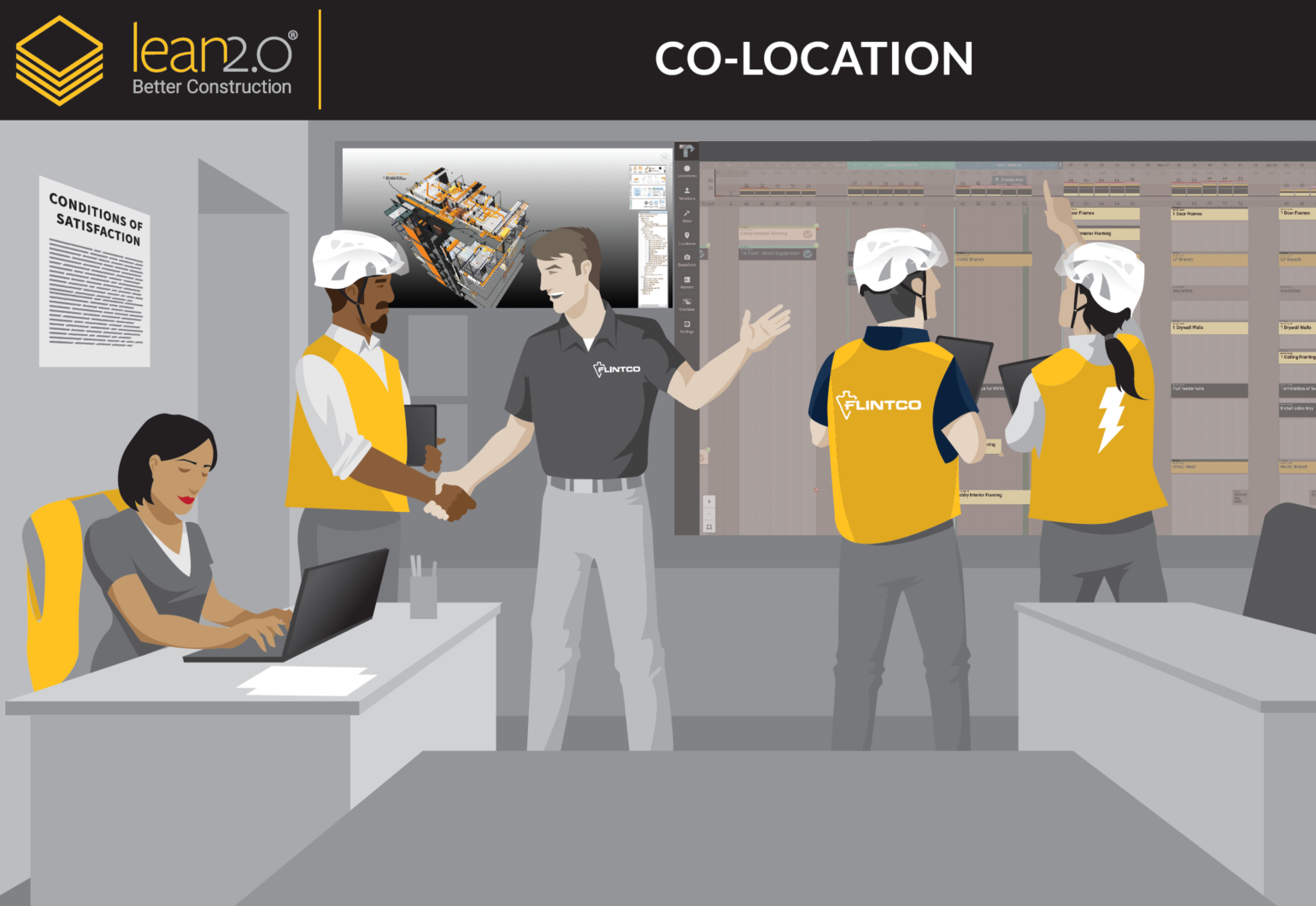
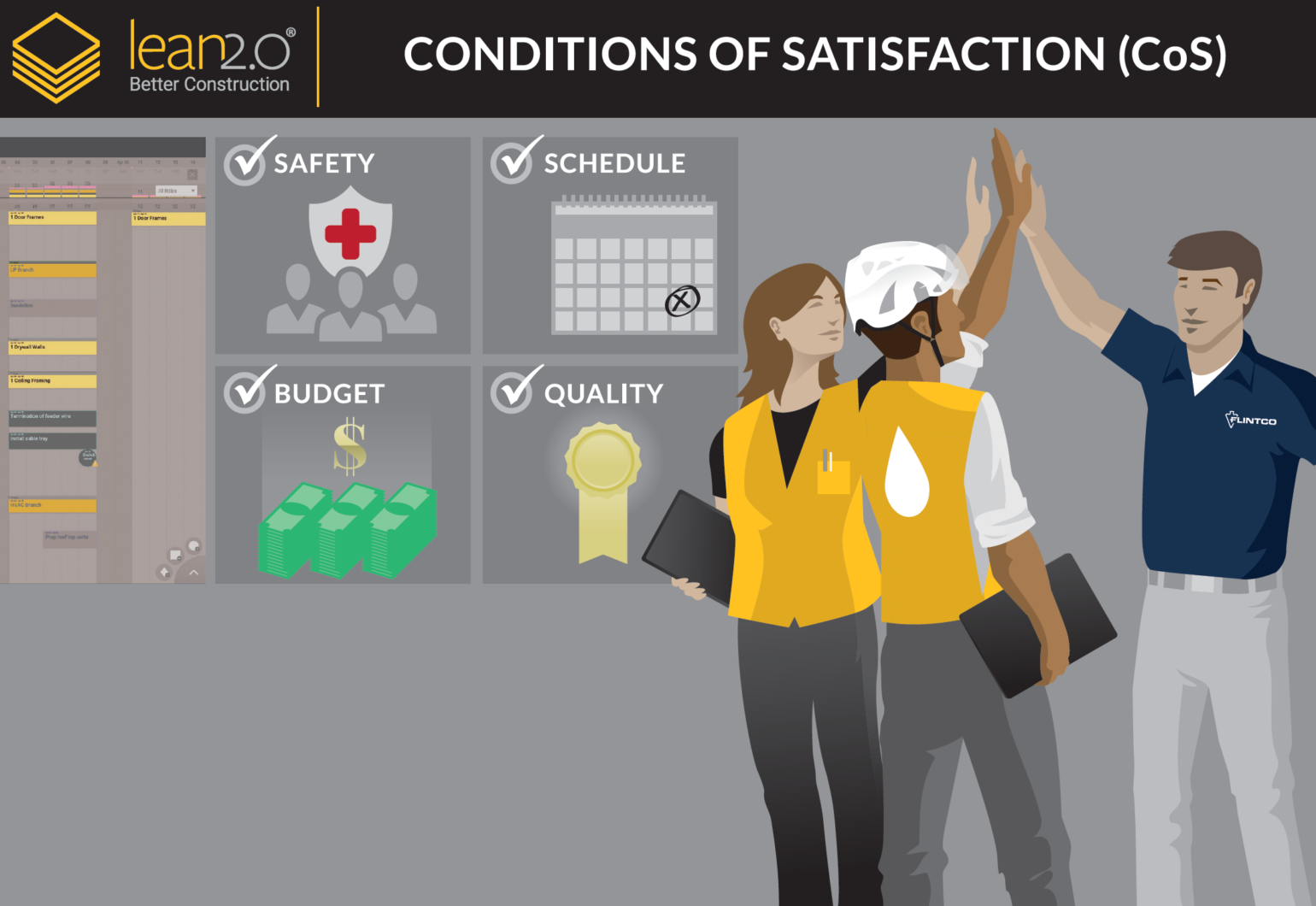
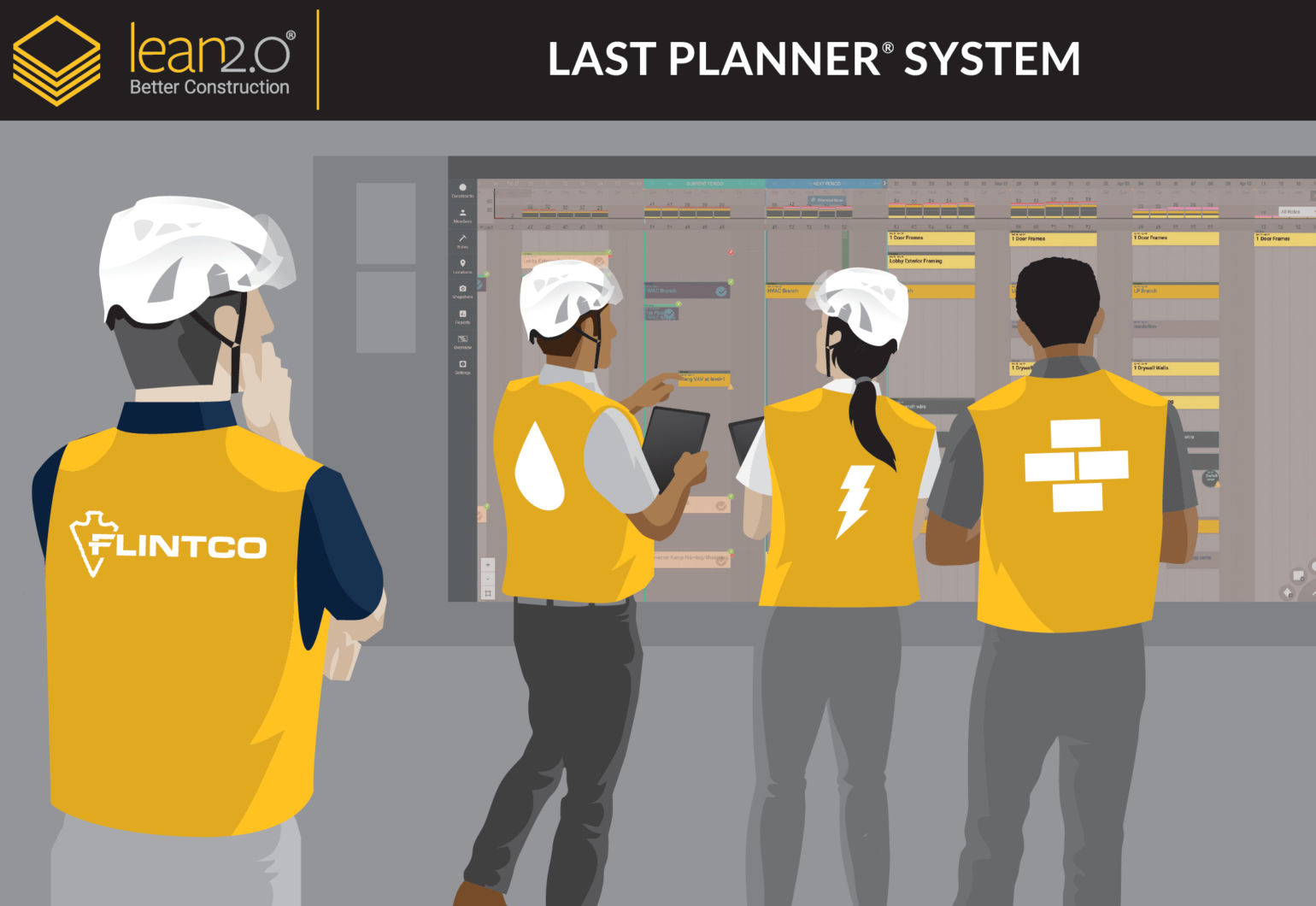
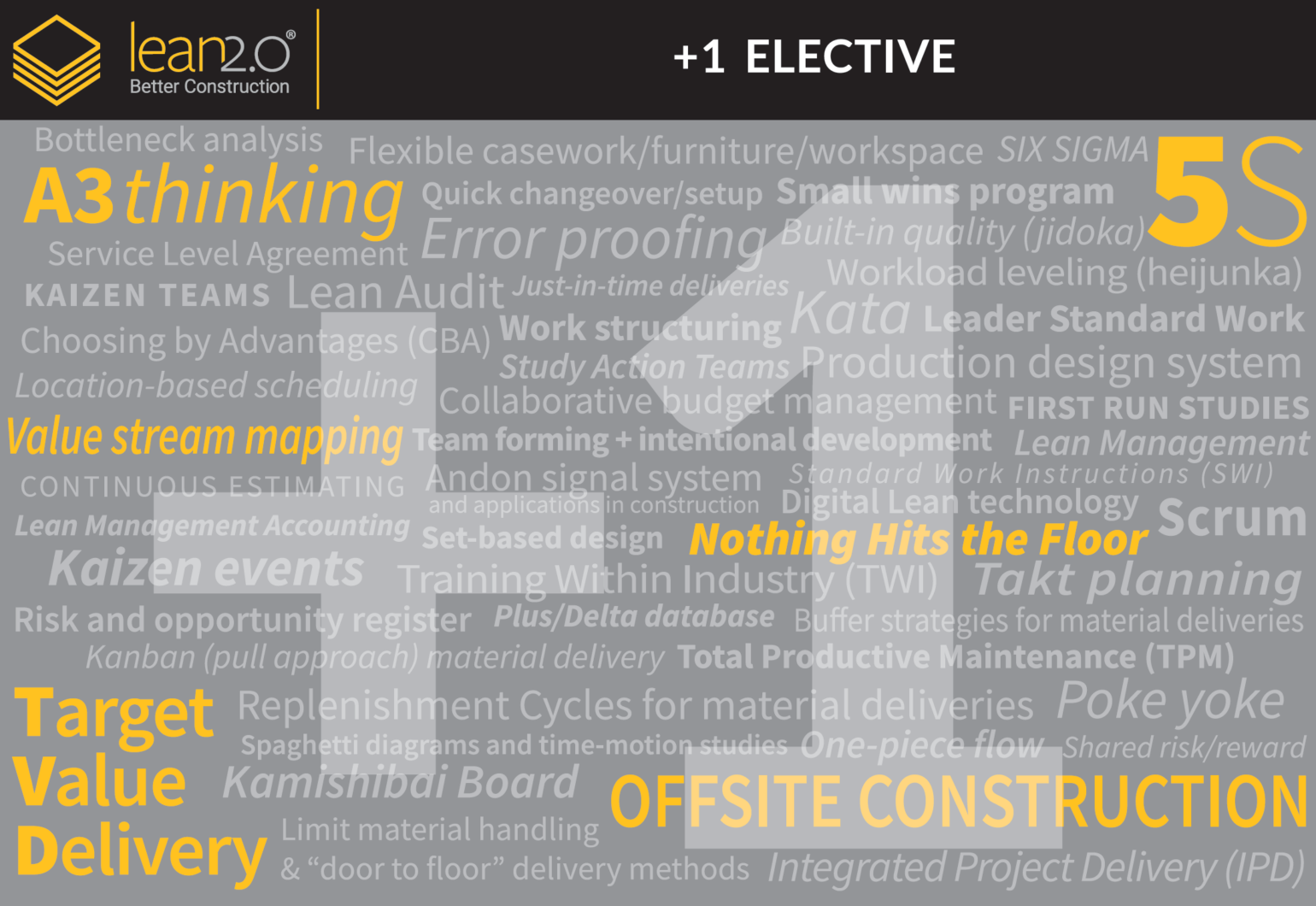
Expert facilitation ensures everyone's voice is heard. Flintco Lean Coaches are subject matter experts who train project teams in Lean start-up and implementation. Everyone on a Lean2.0 project learns how to facilitate a phase plan. Coaches are available for continuous follow-up, which helps sustain Lean2.0 principles throughout the project lifecycle.
Continuous improvement and respect for others defines our approach to Lean. We provide in-house training for owners, A/E team and trade partners on our 5+1 approach that makes Lean2.0 unique. We use a variety of hands-on and virtual simulations to onboard new team members, encouraging a free flow of information to inspire new ideas and continuously learn from each other.
The field office configuration leads to better communication and higher productivity. Is the space conducive to information exchange? Is there room to collaborate comfortably during Last Planner meetings? Can we accommodate a classroom-style meeting? We use visual communication and control, in both digital and analog formats, to bring teams together to improve design and construction outcomes, whether face-to-face or working remotely.
Establishing a unique CoS prior to construction is how we measure success moving forward and the first step in earning a repeat client. Periodic updates with objective measurement and data capture determines if the conditions are being met. We listen to all stakeholders when creating the CoS using a "one team, one goal" approach to remove communication silos.
Creating reliable workflow - the cornerstone of The Last Planner System® - means more project certainty for clients regarding Schedule and Budget. Collaboration and planing with trade foremen lead to buy-in and a happier more productive team. The Last Planner directs the workflow after capturing everyone's input from the field, ensuring the team knows what should-can-will and did get done.
The Flintco Ethos sets us apart. We apply our expanding Lean knowledge and documented best practices to support the Flintco vision: the unwavering pursuit of the perfect construction experience. The +1 Elective is how we "future proof" Lean2.0 by continuously testing and proving additional Lean practices. Through documentation, and sharing among our teams, Flintco is delivering Better Construction for our clients.
Lean by the Numbers
as of 1/2025
Active Lean Projects
Value of Current Lean Projects Underway
Number of Lean Projects Completed
Schedule Performance Better than the Industry Average
Open Projects that are Lean2.0 Projects
Off-site construction is safer, reduces energy consumption and encourages the optimum use of materials.
The practice has many other benefits, including: improved quality, reduced construction waste, shorter schedule durations and is often delivered at a competitive price. We actively work with our trade partners – even on hard bid projects – to find opportunities for offsite construction, which include: exterior wall panels, above-ceiling overhead piping racks, modular central utility plants, modular pump skids, kitted exam rooms and headwalls, restroom pods, MPE riser systems, MPE horizontal distribution systems, electrical rooms and exterior skin components that are prefabricated and pre-assembled into modules off site and ready for installation. Flintco collaborates with specialized trade partners early in a design-assist capacity and uses BIM to build virtual prefabrication models. It’s another way Flintco is delivering Better Construction for our clients.
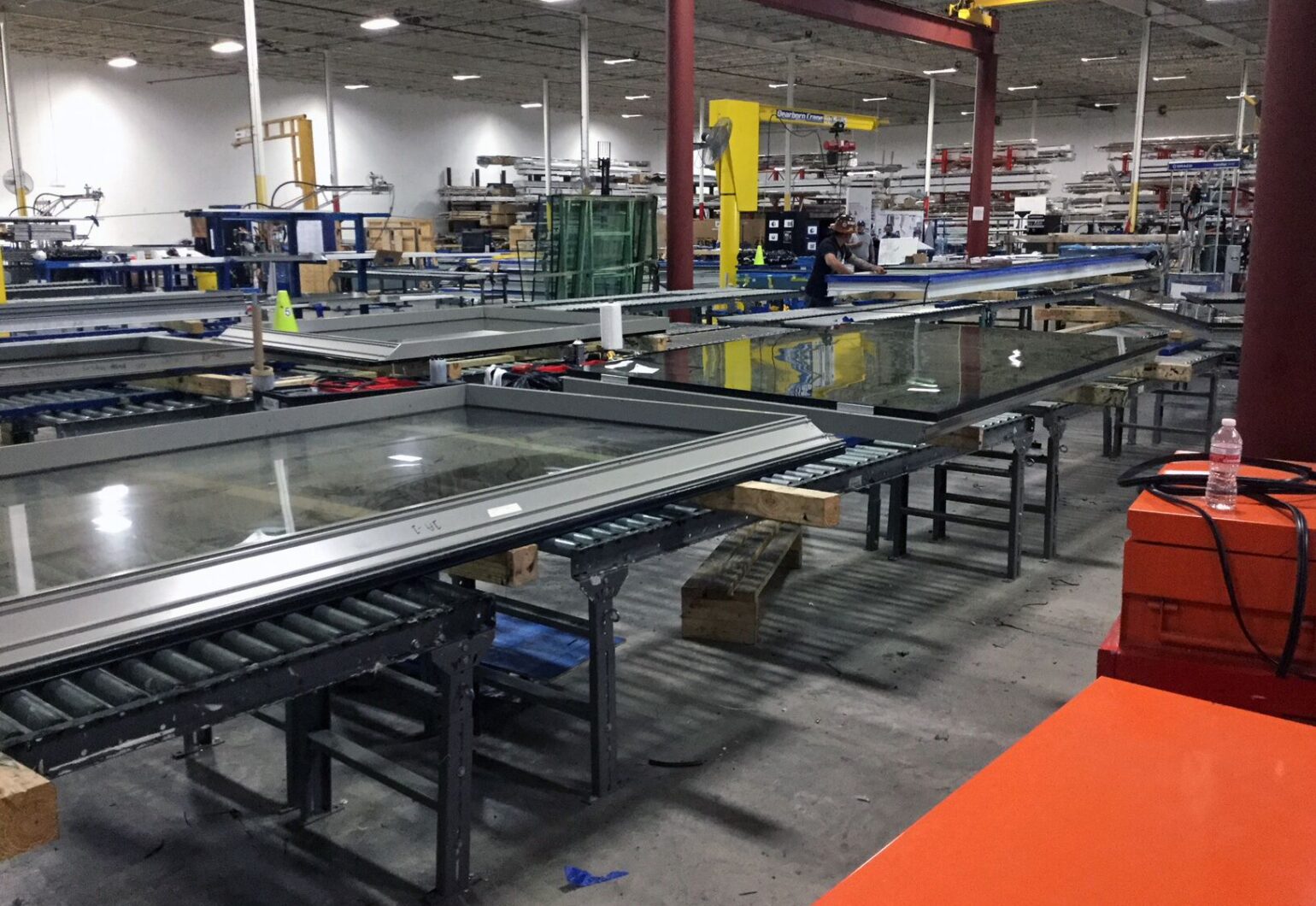
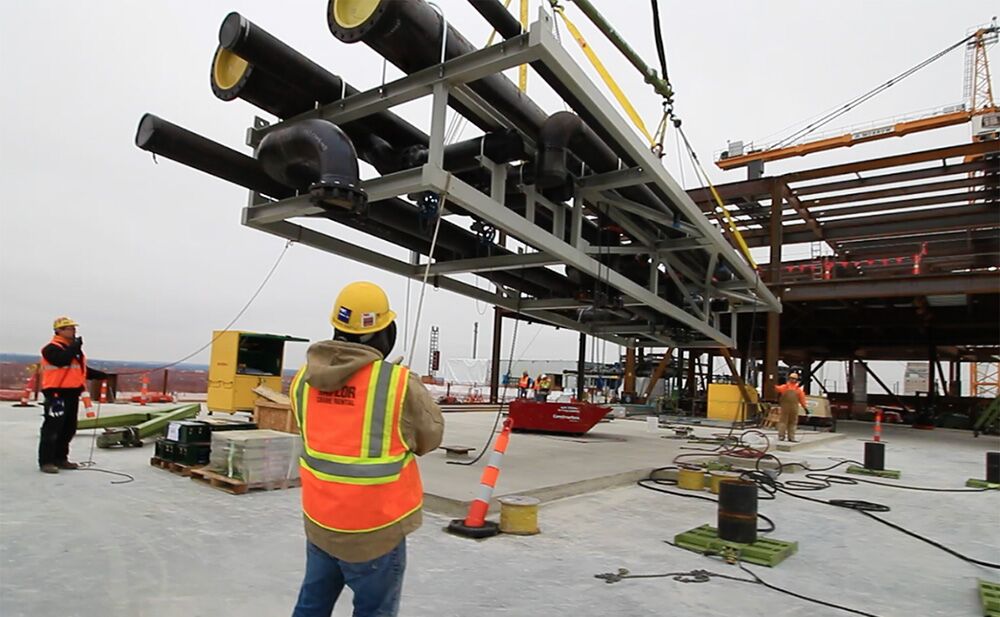
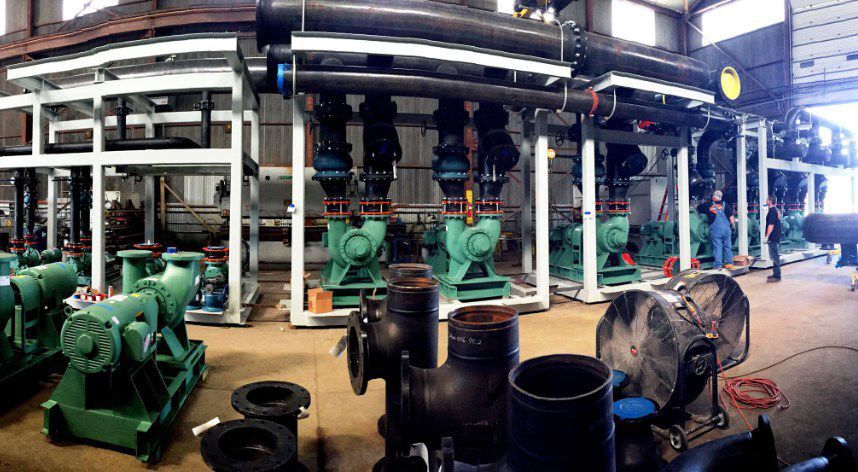
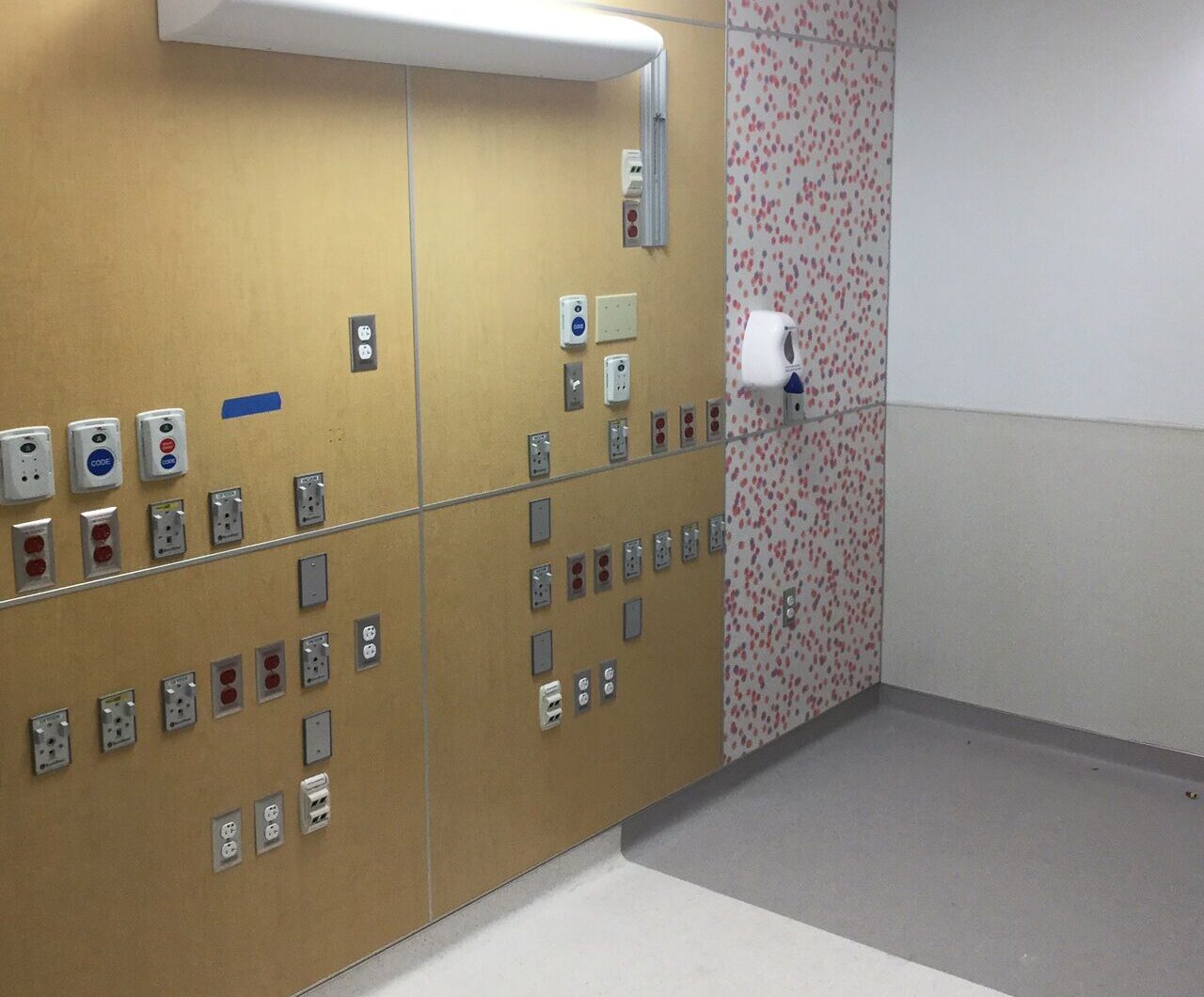